Metal Stamping Procedures: From Prototyping to Mass Production
Metal Stamping Procedures: From Prototyping to Mass Production
Blog Article
The Evolution of Steel Stamping Procedures: Advancements and Applications
The realm of steel marking processes has actually experienced a transformative trip noted by consistent innovation and adjustment to meet the needs of contemporary industrial practices. The applications extend across a range of industries, each profiting distinctly from the improvements in metal marking procedures.
Typical Steel Marking Methods
Traditional metal stamping strategies have long been the foundation of manufacturing procedures in various industries as a result of their performance and accuracy. The procedure involves developing a steel sheet or coil into a desired shape by pushing it in between a die and a punch. This approach is widely utilized for generating big quantities of components with high precision at a quick pace.
One of the essential benefits of typical steel marking methods is the ability to preserve limited tolerances, guaranteeing that each part meets the called for requirements constantly. This degree of precision is necessary in markets such as vehicle, aerospace, and electronics, where even small variances can bring about significant issues.
Additionally, typical steel marking methods use cost-effective options for automation contrasted to other manufacturing approaches. The capacity to mark components in fast succession decreases manufacturing time and decreases labor expenses, making it an attractive choice for organizations aiming to optimize their production procedures.
Appearance of High-Speed Stamping
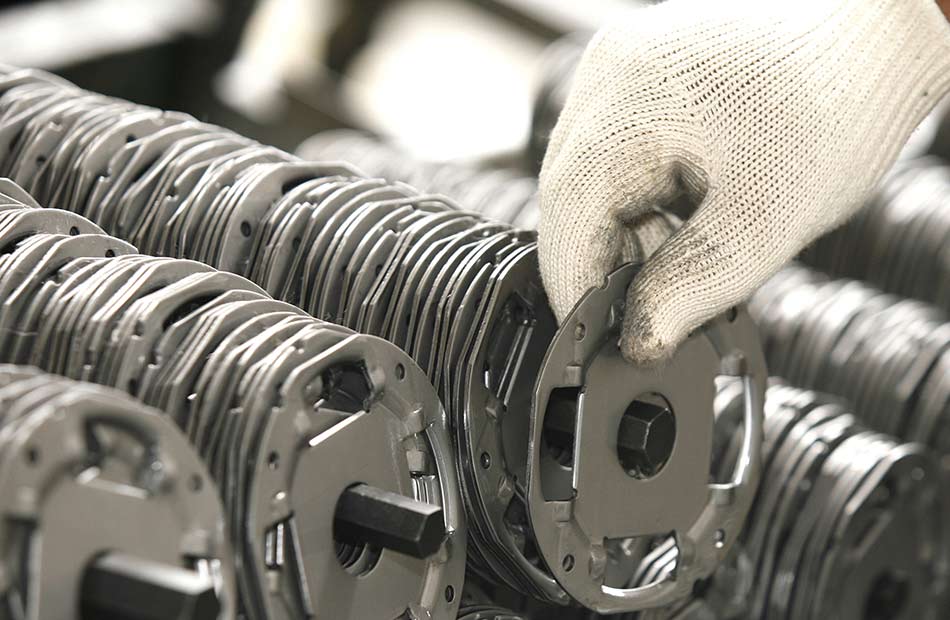
One of the vital benefits of high-speed marking is its capability to preserve precision and consistency even at accelerated processing speeds. This precision is important in industries where limited resistances and detailed styles are needed. Furthermore, high-speed stamping permits the processing of a vast array of materials, including light weight aluminum, stainless-steel, and copper, further expanding its applicability throughout various industries.
Moreover, the pop over here introduction of high-speed marking has enabled producers to meet the growing demand for intricate elements in industries such as automotive, aerospace, and electronics (Metal Stamping). By leveraging the rate and accuracy of high-speed stamping modern technology, firms can boost their competitiveness in a swiftly progressing market landscape
Developments in Tooling Innovation
With the evolution of high-speed stamping allowing boosted accuracy and performance in metal developing procedures, the field of metal marking has seen considerable developments in tooling technology. Tooling technology plays an essential role in metal stamping operations, influencing factors such his explanation as item quality, manufacturing speed, and total cost-effectiveness.
By using these advanced materials, tooling manufacturers can create dies and mold and mildews that hold up against the high pressures and temperatures entailed in click here for info metal marking processes, resulting in longer tool life and enhanced manufacturing efficiency. Overall, these innovations in tooling modern technology have actually transformed the metal marking sector, allowing makers to accomplish higher levels of precision, productivity, and cost financial savings.
Assimilation of Automation in Marking
As automation continues to reshape the landscape of metal stamping procedures, the combination of automated systems has actually come to be progressively prevalent in contemporary production centers. Automated systems supply countless benefits in steel marking, including boosted performance, improved precision, and improved safety. By integrating automation into stamping processes, manufacturers can lower cycle times, reduce material waste, and maximize production throughput.
Among the vital parts of automation in stamping is using robot arms for tasks such as material handling, part adjustment, and quality examination (Metal Stamping). These robotic systems can perform repeated and labor-intensive tasks with rate and precision, liberating human drivers to concentrate on more intricate procedures. Furthermore, automation permits real-time surveillance and modification of marking processes, resulting in greater general process control and quality control
In addition, the integration of automation in marking enables suppliers to attain constant part quality, satisfy limited resistances, and boost total efficiency. As innovation remains to development, the role of automation in metal marking processes is expected to increase further, driving advancement and effectiveness in the production sector.
Applications Across Diverse Industries
Including steel marking processes across varied industries showcases the adaptability and versatility of this production technique. Additionally, the home appliance market advantages from steel stamping processes to make components for fridges, washing makers, and various other household appliances. The flexibility of steel stamping processes makes it a beneficial manufacturing strategy throughout different markets, demonstrating its value in contemporary manufacturing procedures.
Conclusion

Report this page